Roper Whitney Sheet Metal
Folders | Auto Brake AB1014K Kombi Series

Roper
Whitney Autobrake Kombi Series
Kombi Autobrake
For over 40 years, Roper Whitney has been producing
quality folding systems for a variety of markets. Building on
that experience, the newest generation Autobrake folders integrate
advanced wing bending design with the features that have made
the Autobrake the choice of professionals.
The Autobrake combines automated bending of angles up to 145°,
material clamping, and material support into a single CNC controlled
system employing wing bending techniques. Manufacturing, service,
and applications support are based in Rockford, IL U.S.A.
Benefits of the Autobrake System vs. Manual or Press
Brake Bending are:
Reduced labor costs
Improved part accuracy
Reduced setup time
Minimized tool changes
Improved part quality especially on soft and pre-painted material
The Roper Whitney Autobrake is a plate and
weldment steel construction, delivering superior performance
and features in a simplified rigid design. End housings are
a plate-type construction bringing drive components close together
for improved stiffness and performance. Actuating mechanisms
are secured in rigid mounts at the outside of the housings,
allowing easy maintenance.
The unique rotating Kombi beam allows for straight
tooling and Box and Pan tooling. It is a fabricated structural
prism on which is mounted tooling to firmly clamp a broad range
of materials, close hems, and withstand the forces generated
by capacity forming operations. Machined into the Kombi beam
180° from each other are the attachment surfaces for the
straight and box and pan tooling. Tools are attached to the
Kombi beam with standard socket head cap screws. Grooves are
provided to secure tools even while the clamping bars are loosened
for adjustment. Rotation of the Kombi beam is powered by a brake
motor driving a sprocket and roller chain mechanism.
Clamping and hemming are programmed. The upper beam is driven
to program settings on both ends by a brake motor and eccentric
drive of the beam with a connecting shaft. Clamping and hemming
power is delivered to the clamp jaws by a series of spring washers
to provide variable clamping pressures with a shock-absorbing
end stop. This provides reliable clamping pressure regardless
of material thickness. Integral to the upper beam are the ways
with non-metallic gibing to guide and retain the upper beam
within the end housings.
Part program operation and creation are accomplished
on a pendant-mounted computer control, located at the right-hand
side of the machine. Programs are presented in a logical organized
manner similar to the steps used to create parts on traditional
folding brakes, allowing an easy rapid transition to the Autobrake.
The computer control can be rotated into position for best use,
and can be positioned to the rear of the machine.
Programming Functions are:
Bend Angle
Gauging distance
Spring back compensation
Offsets for hem operations
Radius profile macro gauge
Programmable delay for back
Customer alpha/numeric part number
Open hem height
Open, closed, or teardrop hemming entering of part
Information screen for related data
Material handling instructions
Jaw opening
Programmable part counter
Optional Features For The Autobrake Automated
Wing Bender Folder:
- 4" Tall Upper Beam Sectional Tooling
- The unique Kombi beam is a fabricated structural prism
on which is mounted
tooling to firmly clamp a broad range of materials and
withstand the forces
generated by capacity forming operations. Machined into
the Kombi beam 180¡
from each other are the attachment surfaces for the straight
and box and pan
tooling. Tools are attached to the Kombi beam with standard
socket head cap screws
and grooves are provided to secure the tools even while
the clamping bars are loosened
for adjustment. Rotation of the Kombi beam is powered
by a brake motor driving a sprocket
and roller chain mechanism.
- Several Backgauge Configurations Including:
- U-Shaped Backgauge Extension
- The U-shaped 12? backgauge system is simply a right
and left backgauge extension
taking your total backgauge dimension out to 144".
This option can be mounted on any
61" backgauge and can also be added to machine
already in the field.
- Left Or Right Hand 12' Backgauge Extension
- The 12' foot backgauge extension can be added to
any 61" backgauge and will extend your
total gauging out to 144". This feature can be
added at any time and can be retrofitted to
machines that are already in the field. The backgage
extension can be mounted on either the
right or left side but needs to be specified when
it is ordered.
- Complete 12' Backgauge
- The optional complete 12' backgauging system has to
be specified prior to ordering an Autobrake.
This system consists of a complete backgauge table that
is 12' in depth as well as 12' in width.
- 61 inch Sheet Metal Backgauge
- 60" ball screw backgauge offering a larger backgauge
depth as well as the capability to extend the backgauge
to 10'
- Squaring Arm For Small Or Narrow Parts
- A squaring arm can be added to any backgauge to help
in gauging narrow parts.
The squaring arm mounts on the side of the backgauge and
allows the operator to
use one or backgauge fingers to accurately gauge narrow
pieces.
- Laser Scanner
- The optional laser scanner is a programmable safety
system that scans the entire front
side of the Autobrake. This unit is mounted under the
machine and offers more security
than light curtains.
- Hardened Tooling
- Tooling for the Autobrake can be laser hardened for
more durability. This option is only
recommended when all stainless steel or pieces with plasma
cut edges are run on the machine
Specifications For All
Roper Whitney Kombi Autobrakes:
|
AB1016K |
AB1216K |
AB1014K |
AB1214K |
Bending Capacity (Mild Steel) |
16ga |
16ga |
14ga |
14ga |
Bending Capacity (Stainless) |
20ga |
20ga |
16ga |
16ga |
Bending Length |
122" |
147.5" |
122" |
147.5" |
Bending Bars |
0.787", 0.390", 0.250" |
0.787", 0.390", 0.250" |
0.787", 0.390", 0.250" |
0.787", 0.390", 0.250" |
Back Gauge Depth (Standard) |
40" |
40" |
61" |
61" |
Back Gauge Increased (Optional) |
On Request |
On Request |
On Request |
On Request |
Clamping Beam Opening Height |
7.3" |
7.3" |
7.3" |
7.3" |
Clamping Beam Straight Bar Tooling |
30º |
30º |
30º |
30º |
Segment Box and Pan Tooling Depth |
4" |
4" |
4" |
4" |
Folding Beam Adjustment |
2" |
2" |
2" |
2" |
Crowning of the Folding Beam |
5-Point 0"-0.030" Adjustment |
5-Point 0"-0.030" Adjustment |
5-Point 0"-0.030" Adjustment |
5-Point 0"-0.030" Adjustment |
Working Height |
35" |
35" |
35" |
35" |
Machine Length |
155" |
159" |
181" |
181" |
Machine Width |
56" |
89" |
89" |
89" |
Machine Height |
60" |
68" |
68" |
68" |
Machine Weight |
8202lbs |
9542lbs |
10842lbs |
11250lbs |
Shipping Weight |
8912lbs |
10022lbs |
11500lbs |
12000lbs |
Back Gauge Servo Motor |
3/4 hp |
3/4 hp |
3/4 hp |
3/4 hp |
Kombi Beam Rotation Motor |
1 hp |
1 hp |
1 hp |
1 hp |
Clamping Beam Motor |
1.5 hp |
2 hp |
2 hp |
2 hp |
Bending Beam Motor |
1.5 hp |
2 hp |
2 hp |
3 hp |
Return to TOP
Roper
Whitney 1009K Precision Autobrake
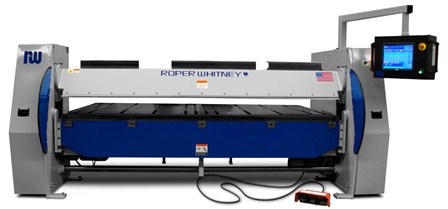
The AB1009K Precision Autobrake provides precision and repeatability when forming up to 10 feet of 9 gauge mild steel or lighter materials. This sheet metal brake is a high speed solution to make a variety of bends while maintaining a high quality level in the end product. The backgauge provides accurate part location through the use of servo drives and is expandable with optional backgauge extensions. The rigid design includes automatic crowning adjustments to ensure accurate bending regardless of raw material stresses. Tooling options are provided to help customize to your specific needs, and can be provided in tool steel or hardened.
Standard Features:
– 30° Clamping Beam
– Hardened 6.3” Quick-Change Kombi Box Tooling
– Hardened Upper Jaw, Lower Jaw & Bending Bars
– Automatic Crowning Adjustment
– Automatic Material Thickness Adjustment
– 61” Backgauge
– Solid Backgauge Fingers
– Adjustable Height Backgauge
– Side Mounted Squaring-Arm
– Automatic Pivot Point Adjustment
– Segmented Bending Beam & Lower Jaw Tooling
– 18.5” Touchscreen Monitor w/ Synergy Control
– Konnect Software Package (Included While Under Warranty)
Options & Upgrades:
– 0.984” / 25 mm Bending Bar
– Left, Right or U-Shaped Backgauge Extensions
– Spring Steel Backgauge Fingers
– Backgauge Ball Transfers (Steel or Acetyl)
– 10’ Safety Laser Scanner
– Second Operator Foot Pedal (Front or Rear)
– Rolling Foot Pedal
– Konstruct Offline Software
The Autobrake design is a plate and weldment steel construction, delivering superior performance and features in a simplified rigid design. End housings are a plate-type construction bringing drive components close together for improved stiffness and performance. Actuating mechanisms are secured in rigid mounts at the outside of the housings, allowing easy maintenance. The bending beam is powered by dual direct drive motors to ensure maximum power and efficiency.
Clamping and hemming capabilities come standard and are already included in the software. Clamping and hemming power is delivered to the clamp jaws by a series of spring washers to provide variable clamping pressures with a shock-absorbing end stop. This provides reliable clamping pressure to create open, tear drop, and closed hems to best suit your needs.
This sheet metal brake comes standard with a rotating Kombi beam. This unique tooling assembly adds to the machines straight and box folding capabilities to produce more complex shapes in less time. It handles a wide range of materials, easily closes hems and withstands the force generated by maximum capacity forming operations. Box tooling is equipped with Roper Whitney’s quick change design allowing for maximum up time and minimized change over time.
Multiple options can be added, at the time of purchase, to maximize the equipment versatility. These options include segmented lower and bend tooling, automated pivot point adjustment, automated up/down backgauge, back gauge extensions for rear operation, and much more. Ask your Roper Whitney sales representative for details.
The Synergy control offers high speed versatility to an end user. It offers multiple methods of programming from simple line-by-line to draw-to-auto program. Its network capabilities allow for multiple options, such as; Konnect, Konstruct, Mobile Konstruct, and overall shop management through linking multiple machines.
Specifications:
Bending Capacity (Mild Steel): 9 ga
Bending Capacity (Stainless): 11 ga - up to 90°, 12ga - past 90°
Bending Length: 126 in
Bending Bars: 1.38" (35mm) bending bar x 150"
& .500" (12mm) bending bar x 150"
Crowning of the Folding Beam: 3-Point 0”-0.030” Adjustment
Folding Beam Adjustment: 2 in
Clamping Beam Opening Height: 7.3 in
Clamping Beam Tooling: 30 Degrees
Back gauge Depth (Standard): 61 in
Working Height: 34 in
Back Gauge Motor: 2.4 hp / 1.8 KW Servo
Clamping Beam Motor: 5.4 hp / 4KW
Bending Beam Motor: Dual 10.8 hp / 8KW
Maximum Depth of Box: (4 Sides) 6.3in
Machine Weight: 17,500 lbs.
Machine Dimensions: 180 x 96 x 84 in
Speeds:
Clamping Beam Speed: 2.5” per second
Folding Beam Speed: 80 degrees per second
Back gauge Speed: (0.25” to 61”) 2.5 seconds
Return to TOP
Return to the Folders
Page
Return to
the New Machinery Page
Return to the Home
Page
|